Wire end ferrules
The key to secure electrical connections
Wire end ferrules are an indispensable component in electrical engineering. They play a crucial role when it comes to making electrical connections safe, stable and durable. With flexible stranded cables in particular, wire end ferrules ensure that the wires do not fray and that the connection in the terminals functions optimally. But what exactly are ferrules and how do you choose the right one?
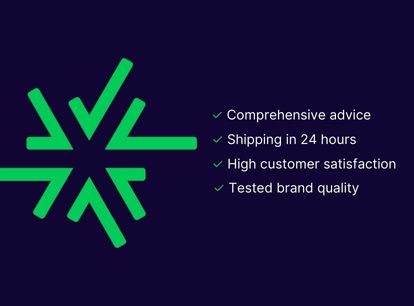
- Comprehensive advice & support
- over 10,000 articles in the shop
- Shipping in 24 hours
- thousands of satisfied customers

KATHRIN BRANDT
Employee Purchasing from TroisdorfGreat advice and friendly service. I was helped immediately and competently with any questions. Gladly again.

OMAR NASER
Office Manager from Frankfurt a.M.Goods are well packaged and arrive safely, which is important to me. My mail was answered immediately.

RAINER SEIDEL
Master carpenter from WiesbadenHad to replace a lamp, but the same was no longer available. Great advice, found a suitable replacement and delivered it quickly.
Light expert info
What are wire end ferrules?
Ferrules are small, tubular sleeves made of metal that are slipped over the stripped ends of stranded wires. Their main purpose is to hold the fine wires of a stranded cable together so that they do not fray when they are inserted into a terminal.
The result is a reliable, low-resistance electrical connection that is both electrically and mechanically stable.
Why are wire end ferrules important?
With stranded wires, there is a risk that the individual fine wires will spread out when connected in a terminal, making the connection unreliable. Wire end ferrules prevent this by bundling and firmly enclosing the wires. This not only ensures better electrical conductivity, but also increases the mechanical strength of the connection. Wire end ferrules are particularly indispensable in applications where high currents or vibrations occur.
Different types of ferrules
There are a variety of ferrules designed for different applications. The most common types include
- Standard ferrules: These simple ferrules are made of tinned copper and are suitable for most standard applications.
- Ferrules with plastic collars: These provide additional protection and prevent short circuits by insulating the metallic part of the ferrule.
- Double ferrules: These special ferrules allow two wires to be crimped in one ferrule. They are ideal for space-saving installations or for double wiring.
- Colored ferrules: To make it easier to identify and find the correct ferrule for specific cable cross-sections, ferrules are available in different colors. Each color code corresponds to a specific cross-section range based on international standards. This makes it easier to select the correct ferrule and helps to avoid errors during installation.
- Special ferrules: For special applications, there are ferrules that have special properties, such as high temperature resistance, special shapes for hard-to-reach areas or designs for very fine or very strong cables. These special ferrules are designed for applications where standard ferrules are not sufficient or not ideal.
Choosing the right wire end ferrule
Choosing the right wire end ferrule depends on several factors:
- Cable cross-section: The size of the ferrule must match the cross-section of the stranded wire. A diameter that is too large or too small can make the connection unsafe.
- Insulated or uninsulated ferrules: Insulated ferrules have an additional plastic collar that provides additional protection and makes it easier to insert them into the terminal. Uninsulated ferrules are simpler and less expensive, but are more suitable for less demanding applications.
- Color code: Ferrules are often color-coded to make the cross-section of the stranded wire identifiable at a glance. This facilitates selection and assignment during installation.
Advantages of wire end ferrules
The use of ferrules has numerous advantages, especially compared to the direct wiring of stranded wires without ferrules:
- Improved safety: by bundling the wires, the risk of short circuits and sparking is significantly reduced.
- Greater mechanical stability: Wire end ferrules serve as kink protection and protect the strands from mechanical stress, vibrations and tensile forces.
- Longer service life of the connection: Connections with ferrules are more durable and more resistant to external influences.
- Easy maintenance: Color-coded ferrules make it easier to identify and replace cables during maintenance.
Areas of application for wire end ferrules
Wire end ferrules are used in numerous areas, particularly in electrical installation, mechanical engineering, the automotive industry and electronics. Wherever stranded wires are used, wire end ferrules are a must to ensure a secure and stable connection. Typical areas of application are
- Distribution boxes and control cabinets: Here, wire end ferrules ensure clean and secure connections that can be easily checked and maintained.
- Building services: In the installation of lighting systems or electrical appliances, wire-end ferrules are essential for creating secure connections.
- Automotive industry: Stable connections are particularly important due to the shocks and vibrations in vehicles. Wire end ferrules provide additional safety here.
Safety aspects and standards
Wire end ferrules must comply with the applicable safety standards to ensure safe use. In Europe, the DIN standard is decisive, which sets requirements for the size, material and processing of ferrules. It is important to use ferrules that meet these standards to avoid short circuits, loose contacts and other potential hazards.
The importance of crimping
Crimping ferrules is an essential step in creating a reliable connection. During crimping, the sleeve is pressed firmly around the strands to create a compact and stable unit. A special crimping tool is used for this, which applies pressure evenly to the sleeve without damaging the strands. A well-crimped end not only ensures excellent electrical conductivity, but also high mechanical strength of the connection.